We support you with innovation
Our mission is to be your digital partner for Sustainability and Efficiency. We drive digital transformation by integrating world-leading process and energy technologies to realize the full efficiency and sustainability opportunities for your business.
The core of what we do

Sustainability
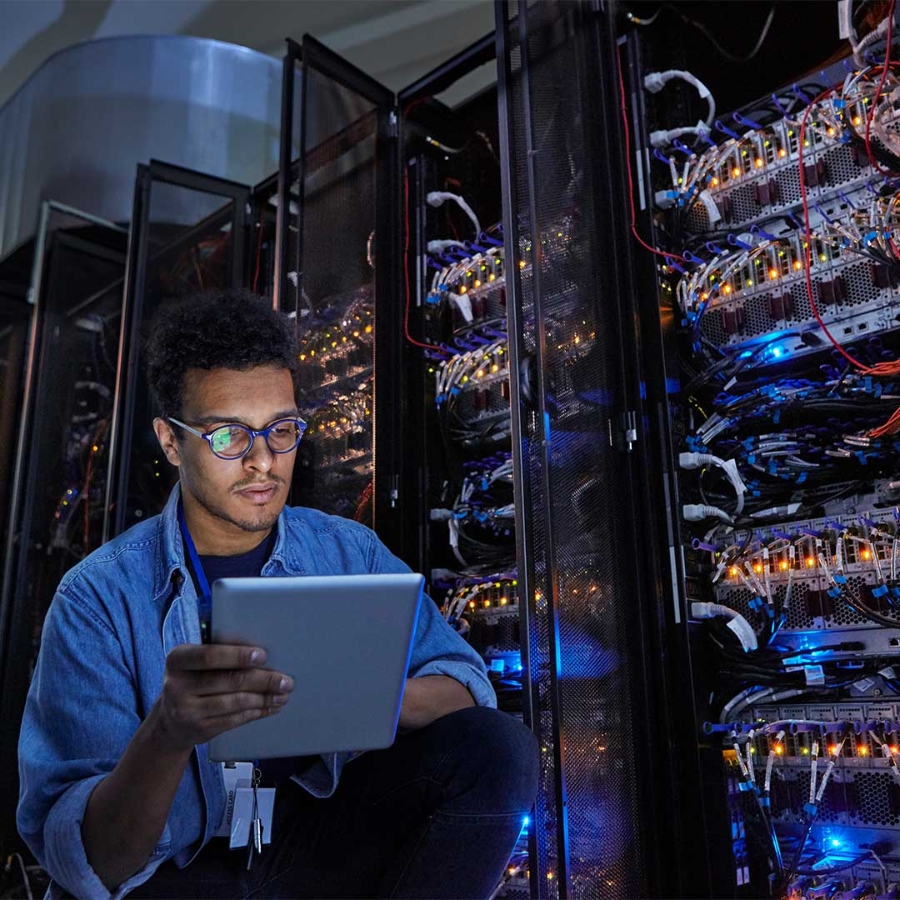
Software
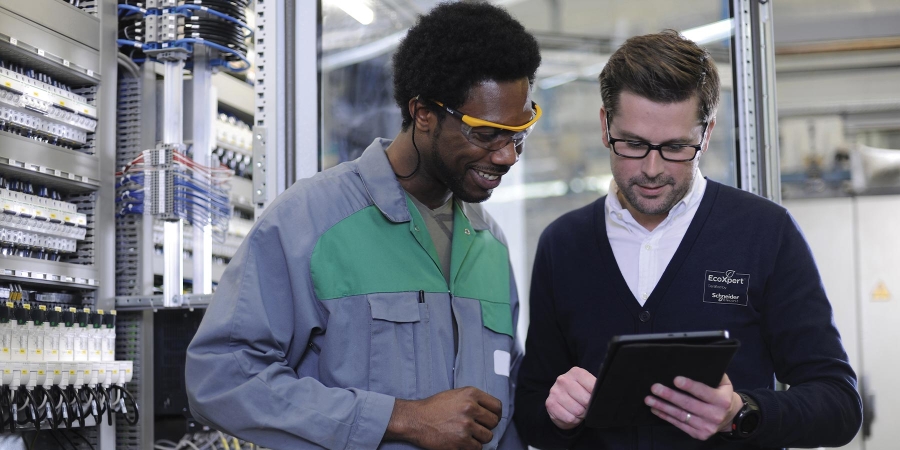
Services
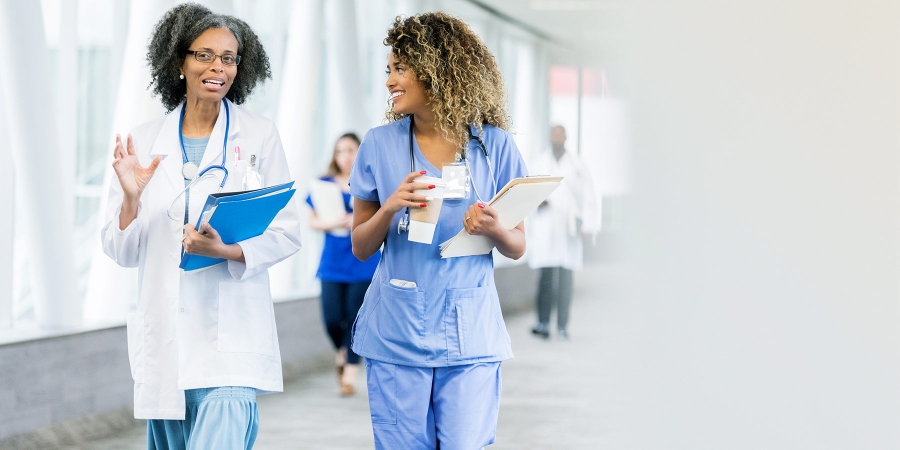
Healthcare
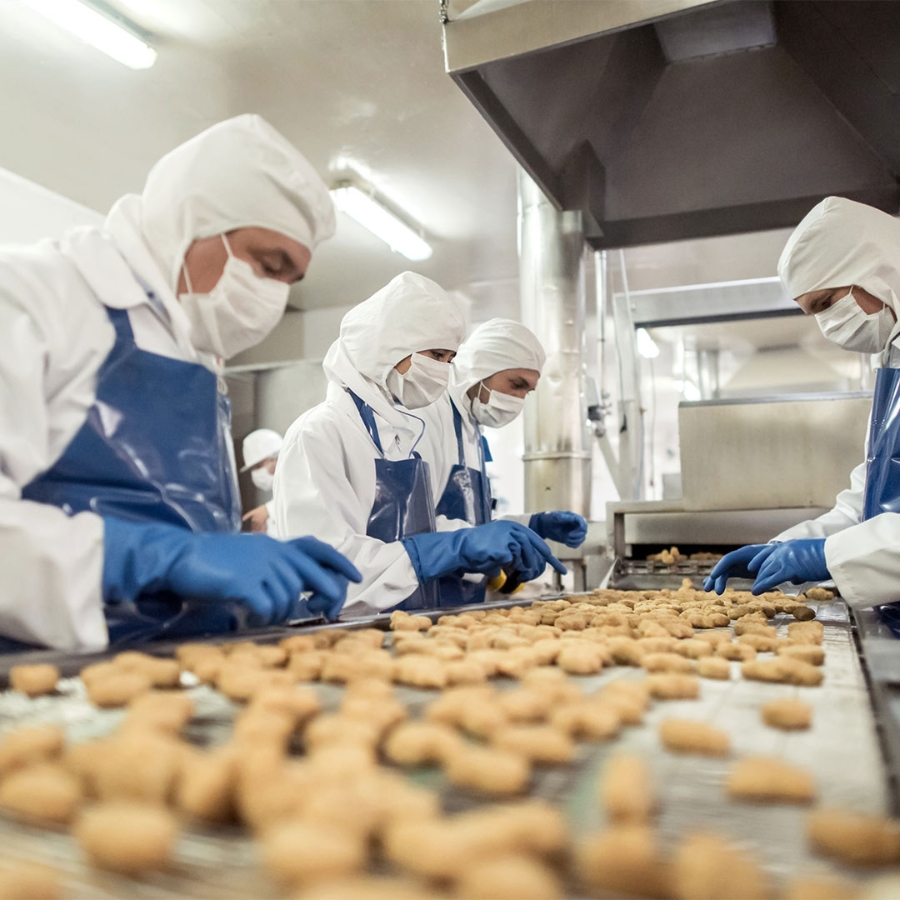
Food and Beverage
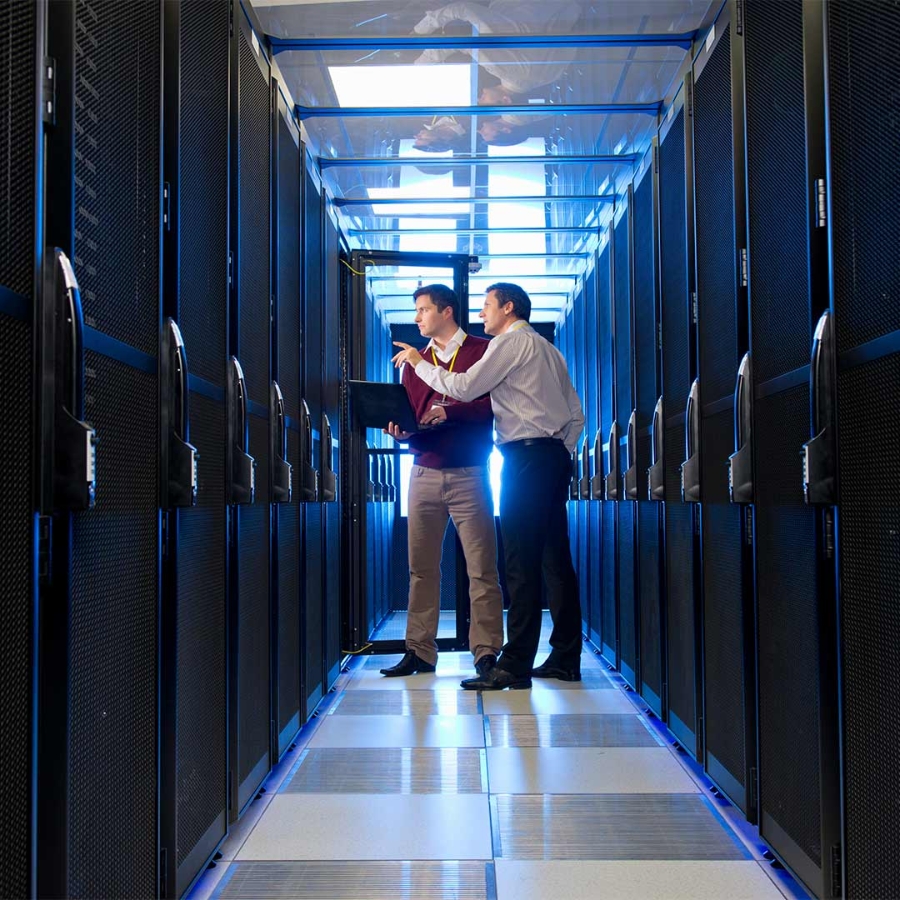